Recyclage : la filière des ballons d'ECS en fin de vie sera opérationnelle début 2026
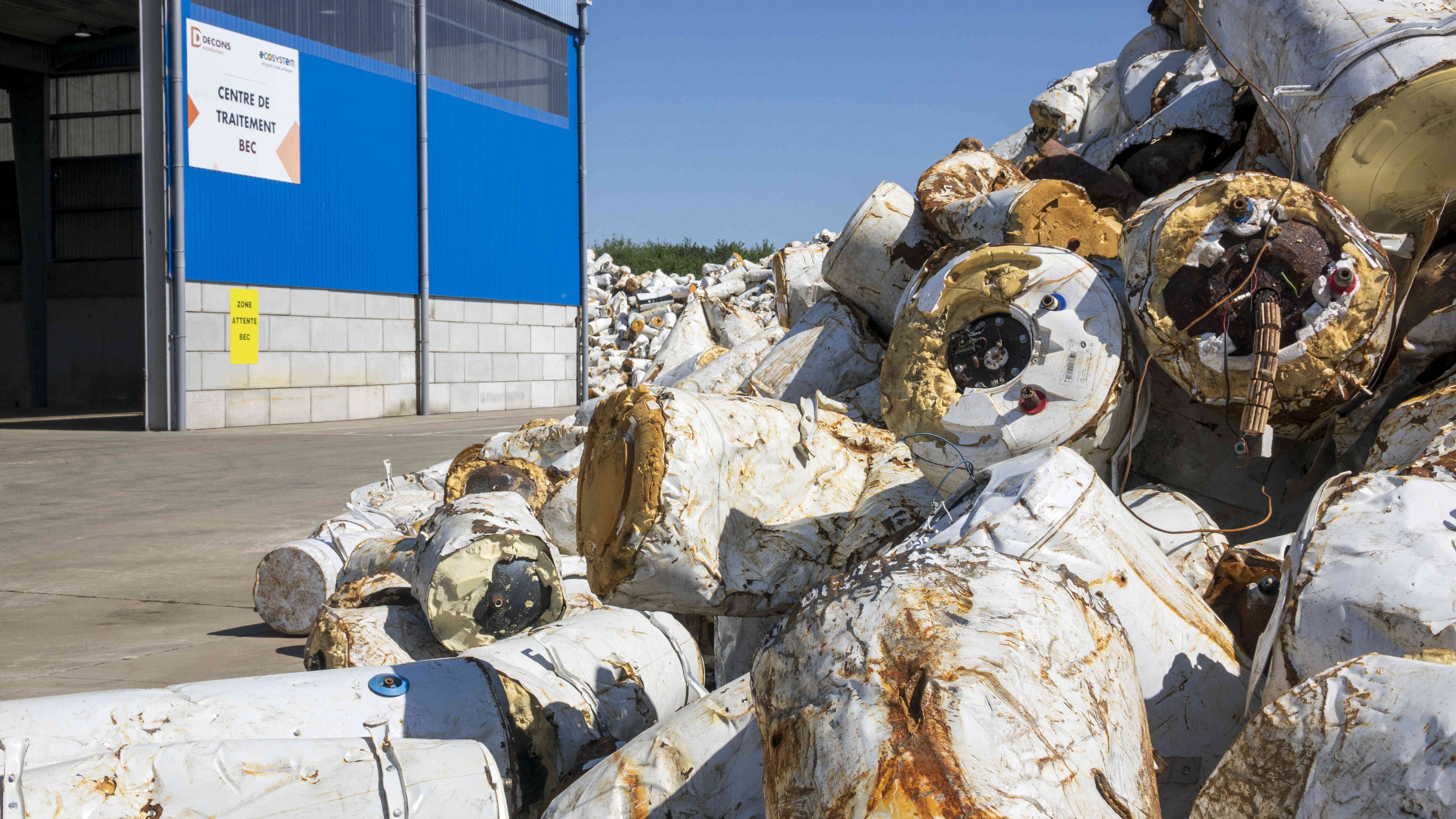
Le cumul des Cumulus est-il en passe d’être réglé ? Dix ans après la loi de transition énergétique qui instituait l’obligation de traitement des ballons d’eau chaude sanitaire, l’organisme EcoSystem dédié à la mise en œuvre de cette REP – responsabilité élargie du producteur – a présenté le 6 mai dernier le premier site de dépollution implanté au Vigeant, dans le sud de la Vienne, sur le site de l’entreprise Decons Récupération.
"C’est le résultat de l’appel à projet lancé en 2022 pour développer une solution industrielle innovante, performante et durable pour la prise en charge des ballons d’eau chaude en fin de vie", commentait Nathalie Yserd, directrice générale d’EcoSystem, lors de l’inauguration de ce nouvel outil industriel.
Un "grain de sable" a bloqué la démarche : le calcaire présent dans les cuves. Initialement estimé à 8% du poids des ballons, ce composant se retrouve en réalité à hauteur de 18-19%. À ce taux, sans pré-traitement, le minéral a pour effet de colmater le flux des matériaux broyés.
La filière de traitement mise au point par l’italien Forrec repose sur une unité de broyage entièrement étanche capable de récupérer le polyuréthene et les gaz à effet de serre qu’il contient. Crédit photo Bernard Reinteau pour XPair
Trouver la bonne méthode
"Nous nous sommes engagés auprès de l’éco-organisme chargé de la dépollution des ballons en 2021", explique Isabelle Savidan, directrice RSE du groupe Atlantic. "Nous avons partagé nos connaissances pour dimensionner le projet et aussi initier un changement de pratique des installateurs et des distributeurs pour orienter les ballons usagés uniquement vers des récupérateurs agréés. L’information sera transmise par les équipes technico-commerciales sur le terrain et à travers nos centres de formation."
Les industriels ont aussi fourni des données élémentaires de marché : parc de ballons, ventes annuelles… Ainsi, on compte en France quelque 16 millions de ballons dont la durée de vie moyenne est de 12-15 ans ; les ventes annuelles sont de 1,9 million d’unités et le gisement à traiter serait de 100 à 120.000 tonnes.
L’autre point dur du traitement des ballons : la présence de près de 10 kg de calcaire fixés sur les parois. Crédit photo Bernard Reinteau pour XPair
Capter les gaz à effet de serre
Au fil des cinquante dernières années, les industriels ont utilisé du CFC (chlorofluorocarbone), du HCFC (hydrochlorofluorocarbone), du HFC (hydrofluorocarbone) et aujourd’hui du penthane (un gaz issu du pétrole). La destruction sans confinement de ces mousses provoque le relargage dans l’atmosphère de chlore, de fluor, de méthane et d’hydrogène.
Autant de gaz à effet de serre (certains sont totalement bannis, d’autres font l’objet de réductions d’usage drastiques) dont les molécules les plus nocives affichent jusqu’à 12.000 équivalent CO2. Ce que les ferrailleurs, jusqu’alors principaux destinataires des vieux ballons déposés par les plombiers et chauffagistes, ne sont pas en mesure de récupérer.
Les aciers sont récupérés par des moyens magnétiques, et les matériaux non magnétiques (cuivre et aluminium) par courant de Foucault. Crédit photo Bernard Reinteau pour XPair
Valoriser tous les composants
De même, la moindre particule de mousse est séparée de l’enveloppe métallique par un broyeur à marteaux, et tout l’isolant est séparé du reste des déchets par une aspiration vers deux silos. Ce stock alimente une machine à pellets ; la mousse, chauffée à 120-130 °C puis pressée, rend ses derniers gaz.
En sortie, les pellets constituent un combustible solide de récupération (CSR) dont le haut pouvoir calorifique de 25 à 35 KJ/kg intéresserait les cimentiers locaux, notamment pour les mélanger à d’autres CSR à bas pouvoir calorifique.
Les gaz à effet de serre (fluor, chlore, méthane et hydrogène) sont comprimés, liquéfiés et mis en bonbonnes pour être expédiés vers un incinérateur de déchets industriels. Crédit photo Bernard Reinteau pour XPair
Composant principal des ballons, l’acier constitue 68-70% du poids des matériaux récupérés. Broyés pour composer une fraction de 0-60 mm, il est capté par des outils magnétiques. Estimé à près de 7.000 tonnes par an, il sera expédié vers des unités métallurgiques en France et en Espagne.
L’installation dispose aussi de moyens pour récupérer les déchets non magnétiques issus du broyage. Des tamis permettent de collecter le calcaire et les plastiques. Actuellement, aucun débouché n’est prévu pour le calcaire.
En outre, des séparateurs à courant de Foucault permettent de distinguer le laiton, le cuivre et l’aluminium ; parmi les refus d’induction, on retrouve aussi de l’inox, des plastiques et des câbles en cuivre. Chaque gisement trié possède sa filière de réutilisation et de recyclage.
Six sites pour couvrir la France
L’installation peut traiter 5 tonnes de ballon par heure, soit 80 à 90 ballons. Son potentiel annuel est de l’ordre de 15.000 tonnes ; selon David Decons, président de l’entreprise, elle peut atteindre 20.000 unités. Par ailleurs, l’entreprise se rémunère sur la revente des produits triés. Le contrat avec EcoSystem est d’une durée de six ans.
Après Le Vigeant en mai, une deuxième unité sera mise en service le 25 juin par le hollandais Coolrec à Lesquin (59), une troisième par Derichebourg à Bonneuil-sur-Marne (94) le 17 septembre, deux autres par Derichebourg à Cheminot (près de Metz, 57) et à Saint-Pierre-de-Chandieu (près de Lyon, 69) au second semestre, et une dernière par Derichebourg près de Nantes (44) au 1er semestre 2026.
Les mousses sont chauffées et pressées pour les débarrasser de la totalité des gaz qu’elles contiennent, puis compactées en granulés pour servir de combustible à haut pouvoir calorifique. Crédit photo Bernard Reinteau pour XPair
Ces unités de taille équivalente à celle présentée au Vigeant sont chacune dédiés à un territoire défini par EcoSystem. L'éco-organisme est aussi chargé de traiter d’autres déchets tels que les ballons thermodynamiques en vente depuis les années 2000.
Au Vigeant, la deuxième moitié du hall industriel dédié par Decons au pôle "ballons d’eau chaude" sera occupé par une filière dédiée à cette famille de produit dès 2026. Elle intégrera la récupération des gaz frigorifiques et le recyclage des petites pompes à chaleur.
Lire aussi
-
Déchets du bâtiment : la filière génie climatique salue le moratoire sur la Rep PMCB
-
L'hybridation des solutions, la prochaine étape dans la transition du CVC ?
-
Comment ce boîtier intelligent permet de réduire de 25% la consommation des chauffe-eau électriques
-
Chauffage : la pompe à chaleur hybride en quatre questions
Sélection produits
Contenus qui devraient vous plaire
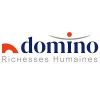
- Domino RH Béziers
Plombier Climaticien (H/F)
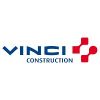
- VINCI Group